Introduction - The Need for Simulation in Semiconductor & High-Tech Industries
Semiconductor and high-tech products are among the most intricate to design and manufacture. These devices often contain microscopic components, such as microchips, sensors, and high-density electronic circuits, which are delicate and prone to failure under mechanical, thermal, or electrical stress.
Additionally, as the trend moves toward miniaturization, product designs are becoming increasingly compact and complex, making physical prototyping both time-consuming and costly.
To ensure reliability, product engineers must validate their designs before production. Traditional trial-and-error testing methods are no longer viable due to cost and time constraints. By leveraging advanced virtual testing environments, engineers can predict product performance, optimize design and development processes, minimize warranty risks, and ensure compliance with industry standards.
This blog explores key aspects of simulation that are critical for semiconductor and high-tech product development:
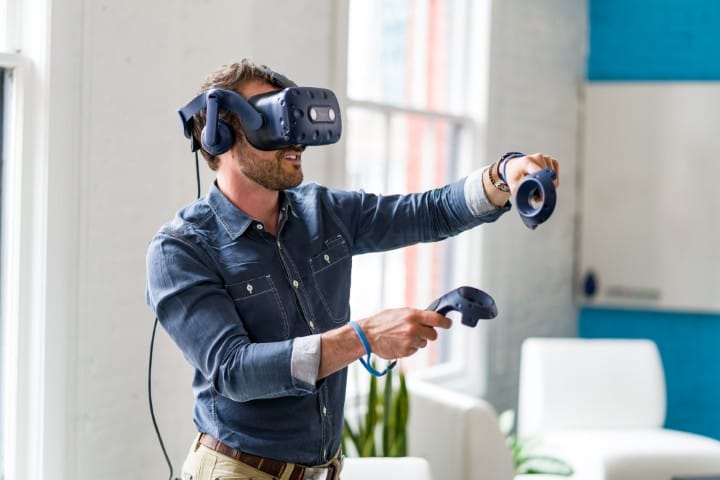
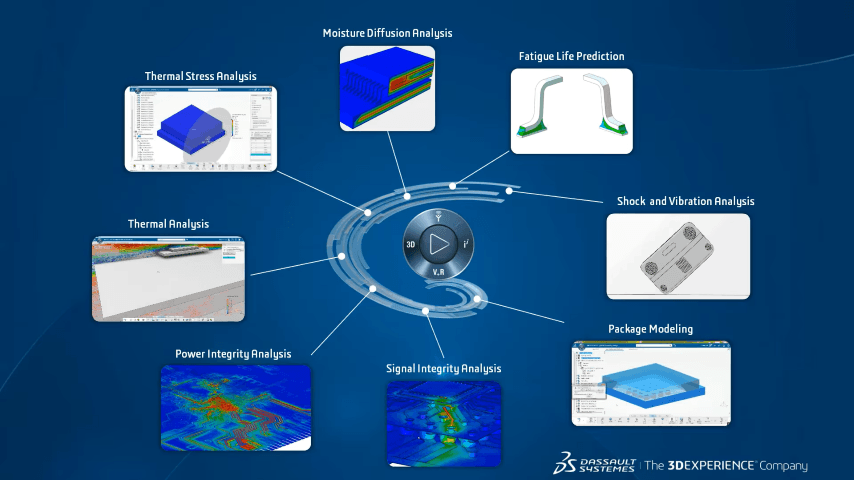
Packaging Modeling & Structural Integrity Analysis
The housing or casing of a semiconductor or high-tech product – often referred to as the package – provides structural support and protection for internal components. Unlike external packaging used for shipping, this structural enclosure is integral to the device’s functionality, incorporating wiring, circuit boards, cooling mechanisms, and other essential parts.
During the conceptualization phase, designers aim for a sleek and compact form factor, particularly for consumer electronics. However, aesthetics must not compromise durability. Packaging modeling combined with simulation ensures that the CAD model meets mechanical reliability standards. Here are some critical structural simulations commonly conducted:
- Modal Analysis – Identifies natural frequencies of the structure, helping to prevent unwanted resonance that could lead to failure.
- Vibration Analysis – Predicts the effects of mechanical vibrations over time, crucial for products exposed to transportation stress or operational movements.
- Drop Test Simulation – Evaluates the impact resistance of a product when dropped from various heights, angles, and onto different surfaces.
- Fatigue Life Prediction – Assesses material wear over repeated loading cycles, ensuring long-term durability of the casing and internal components.
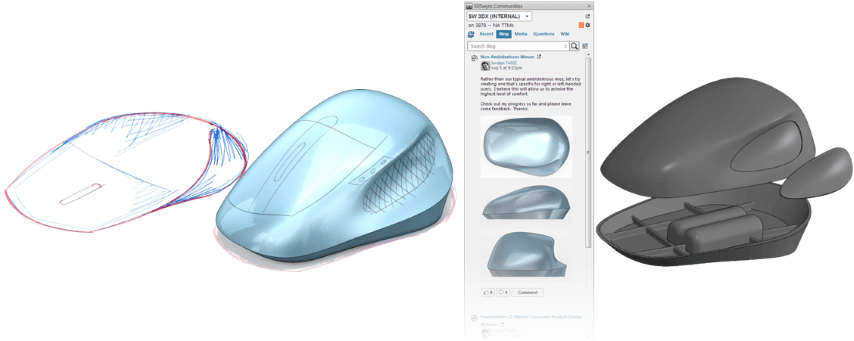
Electromagnetic and Signal Performance Analysis
Electromagnetic compatibility (EMC) refers to an electronic device’s ability to function properly in its environment without causing interference to other devices. The heart of any high-tech product lies in its ability to process and transmit data efficiently. Ensuring EMC and optimal signal performance is critical, particularly in semiconductor devices, wireless communication products, and high-speed computing systems.
Electromagnetic simulations help engineers analyze:
- Signal Integrity – Ensures that high-speed signals maintain their integrity without excessive distortion or noise.
- Electromagnetic Interference (EMI) Compliance – Evaluates whether a device meets regulatory standards for electromagnetic emissions, preventing interference with other electronics.
- Shielding Effectiveness – Tests the efficiency of enclosures in blocking external electromagnetic fields, protecting sensitive components from interference.
Managing electromagnetic performance, including EMI, is a crucial aspect of product development, as all devices must comply with international EMC standards governing emissions and susceptibility.
Engineers tasked with balancing quality requirements alongside design constraints such as size, cost, and performance can significantly simplify this challenge by addressing electromagnetic issues early in the design process. Early identification optimizes various design aspects such as printed circuit board (PCB) layouts, antenna placement, and shielding strategies.
Thermal and Thermal Stress Analysis
Overheating remains a major challenge in semiconductor and high-tech products, often revealing itself in ways that consumers can easily notice. Symptoms of poor thermal design include battery swelling, noticeable drops in performance, and excessive surface temperatures. More concerning, however, are serious safety risks such as fire hazards or even explosions.
At a technical level, inadequate heat management can lead to issues like solder joint fatigue, PCB delamination, and thermal expansion mismatches, all of which compromise structural integrity and functionality. Excessive heat buildup accelerates material degradation, shortens component lifespan, and, in severe cases, results in complete device failure.
To mitigate these risks, effective heat dissipation strategies must be integrated early in the design process. By leveraging thermal simulation tools, engineers can predict temperature distribution across a device and optimize cooling solutions to ensure long-term reliability and safety.
Some key thermal analyses include:
- Conduction, Convection & Radiation Studies – Determines how heat transfers within and away from the device.
- Heat Sink Optimization – Identifies the best design for dissipating heat efficiently.
- Thermal Stress Analysis – Assesses how thermal expansion and contraction affect material integrity, preventing warping or cracking under temperature fluctuations.
- Joule Heating Analysis – Evaluates heat generation in electrical components due to current flow, helping prevent overheating and ensuring efficient thermal management.
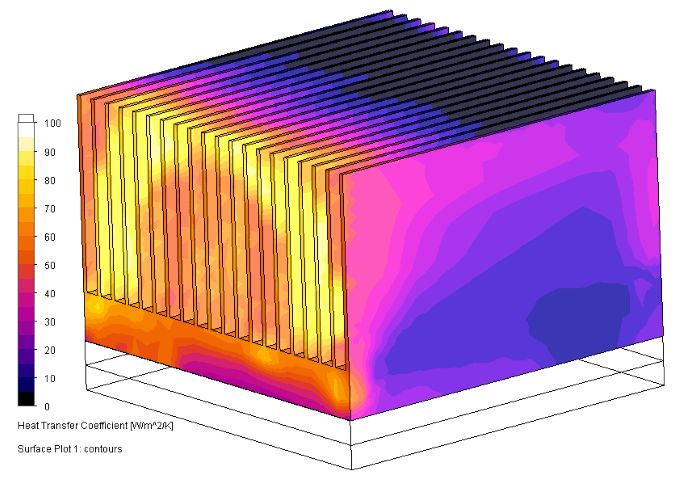
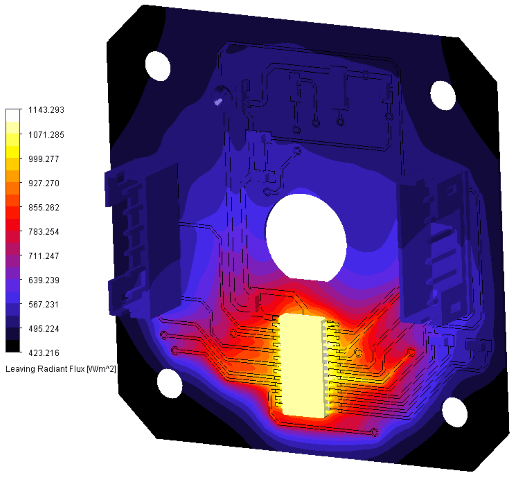
Other Simulations to Ensure Product Reliability
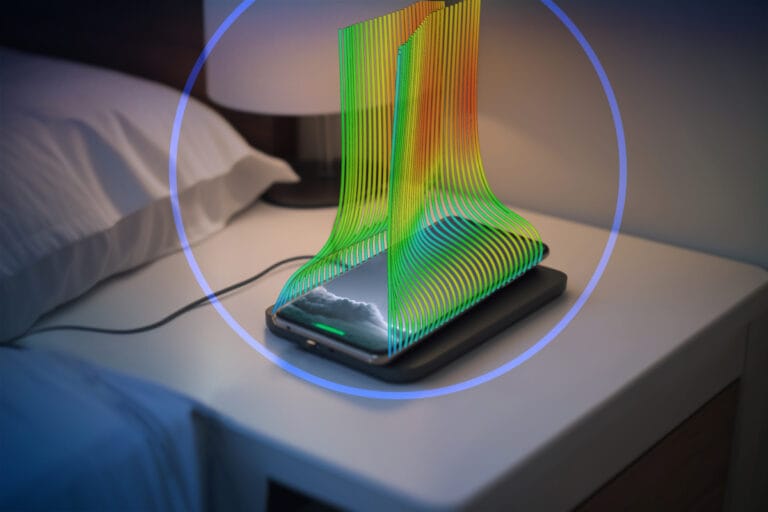
Beyond structural, thermal, and electromagnetic analyses, here are some other factors that play a key role in product reliability:
- Power Integrity & Electrical Performance – Ensures stable power distribution to minimize voltage drops, heat buildup, and efficiency losses in electrical circuits and battery systems.
- Moisture Diffusion Analysis – Predicts moisture absorption in semiconductor materials, preventing corrosion, short circuits, and long-term degradation in humid environments.
Conclusion – Go Smarter, Faster, and Greener
In the rapidly evolving semiconductor and high-tech industry, the demand for rigorous product validation has never been greater. With devices becoming smaller, faster, and more complex, ensuring reliability and performance before manufacturing is critical to staying competitive.
Beyond performance, sustainability is also a driving force in modern engineering. Simulation enables engineers to reduce reliance on physical prototyping, minimizing material waste and lowering the environmental impact of product development.
The power of cloud-based platforms further enhances this process, allowing teams to collaborate seamlessly, manage vast datasets, and streamline project workflows. By leveraging 3DEXPERIENCE Works Simulation, companies can drive innovation with smarter, more efficient, and sustainable design validation.
Talk to CADVision Systems for end-to-end engineering consultation and services, including design and simulation, to help you develop reliable, high-performance semiconductor and high-tech products. Contact us at [email protected] today.
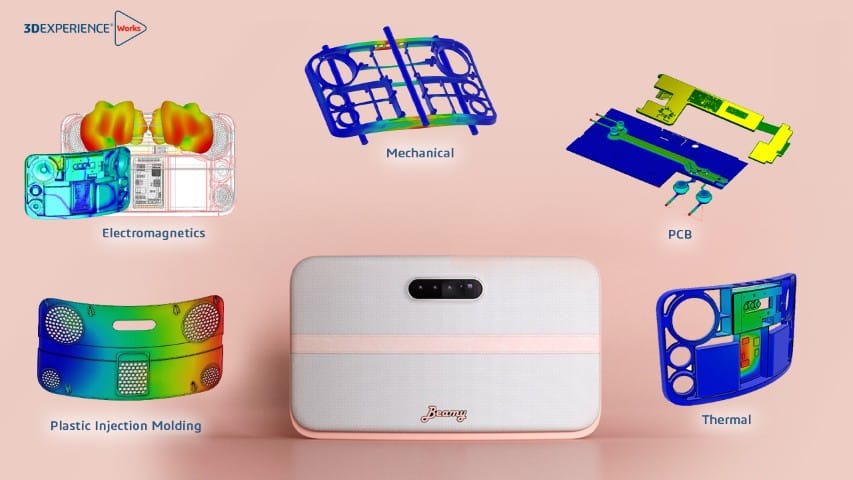