Why Thermal Management Is No Longer Optional
In today’s fast-paced world of compact electronics and high-performance devices, thermal management is no longer an afterthought—it’s a design necessity.
Whether you’re building LED lighting systems, consumer electronics, or dense printed circuit boards (PCBs), heat can be the silent killer—degrading performance, shortening lifespan, or even leading to catastrophic failures.
That’s where SOLIDWORKS Simulation comes in. With advanced thermal analysis tools, it empowers engineers to predict, visualize, and optimize heat transfer at an early stage of product development. In this article, we’ll dive into the fundamentals of conduction, convection, and radiation, and how SOLIDWORKS Simulation helps you tackle each heat transfer mode effectively.
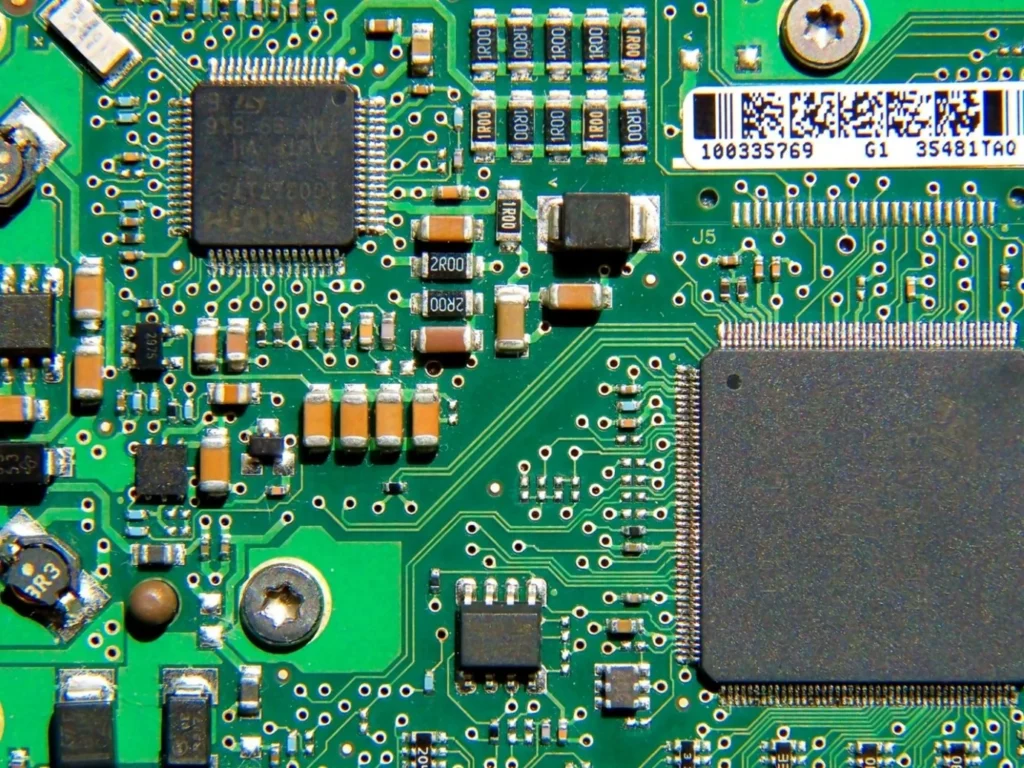
Why Thermal Analysis Matters
Overheating is a top concern in modern product design, especially in electronics. Here’s why you need to take it seriously:
✅ LEDs lose brightness and efficiency when temperatures rise.
✅ Battery-powered devices suffer reduced performance and shorter battery life.
✅ PCBs and microchips can be permanently damaged by thermal hotspots.
As power density increases, effective thermal management becomes even more critical. Traditional trial-and-error prototyping is costly and inefficient—thermal simulation offers insight before a single prototype is built.
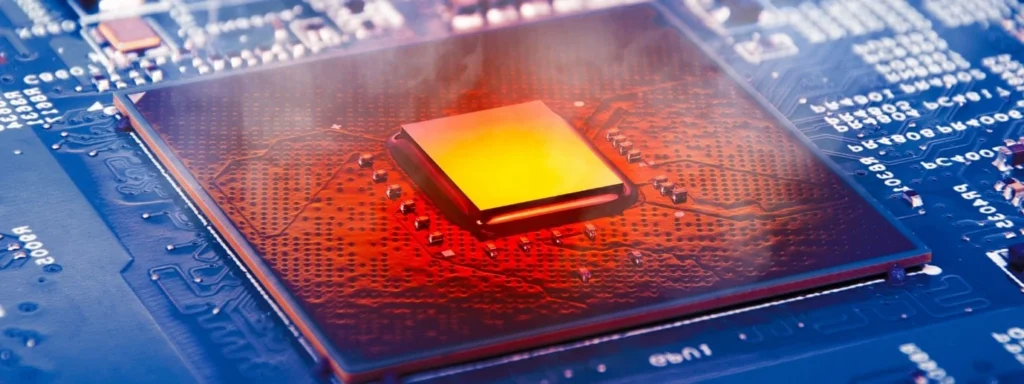
Mastering Heat Transfer: The 3 Pillars
To control temperature, you must understand the three mechanisms of heat transfer: conduction, convection, and radiation.
1. Conduction – Heat Flow Through Solids
Conduction is the transfer of heat through solid materials like copper, plastic, or aluminum. In SOLIDWORKS Simulation, you can model heat flow through components such as a PCB or aluminum casing by assigning thermal conductivity values to materials, helping you assess how effectively a heat sink dissipates heat from critical components.
2. Convection – Airflow Cooling Your Design
Convection is the transfer of heat from a surface to a moving fluid, such as air or liquid, and can occur naturally through passive airflow or be forced using fans or pumps. In SOLIDWORKS Simulation, you can model airflow within electronic enclosures to determine whether your design—using fans, vents, or airflow channels—provides sufficient cooling for components like processors, batteries, or power modules.
3. Radiation – Heat Transfer Without Contact
Radiation is the transfer of thermal energy via electromagnetic waves, even through a vacuum, and becomes especially important in enclosed or high-temperature environments. In SOLIDWORKS Simulation, be sure to include surface emissivity and view factors to accurately evaluate radiative heat loss—crucial for applications like LED lighting or compact electronic housings.
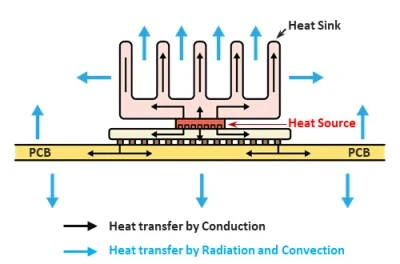
Key Benefits of Using SOLIDWORKS Simulation for Thermal Studies
With SOLIDWORKS Simulation, you can conduct both steady-state and transient thermal analysis to answer vital questions:
- Which components are at risk of overheating?
- Do I need a heat sink or thermal interface material (TIM)?
- Will passive cooling suffice, or is active cooling required?
- How does temperature vary over time with power cycling?
Notable Features:
- Simulate thermal interface resistance between surfaces
- Assign accurate material thermal properties
- Combine thermal and structural analysis to study thermal stress and deformation
- Integrate with SOLIDWORKS Flow Simulation for advanced fluid-thermal coupling in forced-air or liquid-cooled systems
Thermal issues are often invisible—until they cause failure.
But with SOLIDWORKS Simulation, you gain the power to anticipate and resolve thermal challenges early in the design cycle.
Whether you’re engineering the next-gen gadget, lighting innovation, or compact IoT solution, optimizing your product’s thermal performance ensures it runs cooler, lasts longer, and delights your users.
Get in touch with our team to explore how SOLIDWORKS Simulation can help you stay cool under pressure.