SOLIDWORKS Simulation is a powerful solution that helps engineers validate designs, reduce physical prototyping, and enhance product performance. But even experienced users can fall into common pitfalls that compromise results or waste valuable time.
Whether you’re new to simulation or a seasoned user, avoiding these mistakes can significantly improve your outcomes. Here’s a look at the most frequent errors—and how to prevent them.
1. Skipping Material Properties Setup
- The Mistake:
Jumping into a simulation without defining or verifying the material properties—sometimes even using the wrong material. - Why It Matters:
Material data directly affects stress, strain, and thermal performance. An inaccurate material setup can completely invalidate your simulation. - How to Avoid It:
Always verify material properties under Simulation > Study Material. Use the built-in SOLIDWORKS material library, or import precise data from material suppliers when necessary.
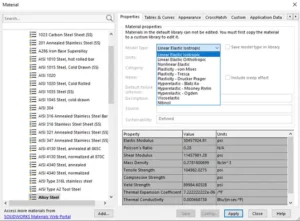
2. Over-Simplifying or Over-Complicating the Model
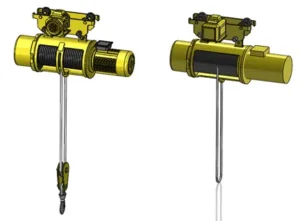
- The Mistake:
Using a model that’s too detailed (e.g., unnecessary fillets or holes) or overly simplified (missing crucial geometry or interfaces). - Why It Matters:
Too much detail slows down computation, while too little detail can produce misleading results. - How to Avoid It:
Use defeature tools to remove irrelevant details, but keep essential elements—especially connection interfaces and areas of high stress.
3. Incorrect Boundary Conditions
- The Mistake:
Incorrect or missing loads and fixtures that don’t reflect real-world conditions. - Why It Matters:
Boundary conditions define how your model behaves under load. Unrealistic setups lead to inaccurate conclusions. - How to Avoid It:
Base your setup on real-world scenarios. Double-check load directions, units, and magnitudes before running the study.
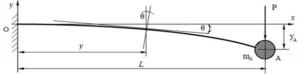
4. Neglecting Mesh Quality
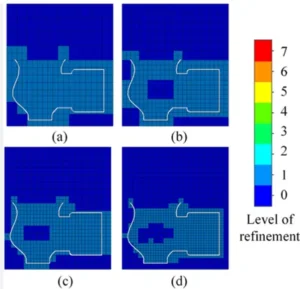
- The Mistake:
Relying entirely on automatic meshing without reviewing mesh density or convergence. - Why It Matters:
A poor mesh can miss critical stress points or lead to convergence errors. - How to Avoid It:
Use mesh controls in high-stress areas and perform a mesh convergence study to ensure your results are stable and reliable.
5. Ignoring Contact Definitions
- The Mistake:
Assuming touching parts in an assembly will interact as expected by default. - Why It Matters:
Without proper contact settings, parts might behave as if they’re bonded or pass through each other. - How to Avoid It:
Explicitly define contacts—such as no penetration, bonded, or allow separation—based on how the parts interact in real life.
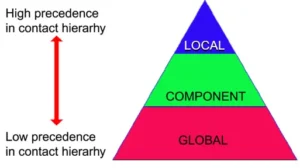
6. Misinterpreting Results
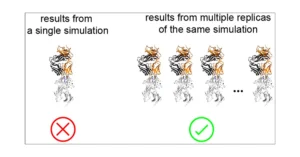
- The Mistake:
Taking stress or displacement plots at face value without understanding the context. - Why It Matters:
Simulation plots can be deceptive if you overlook critical factors like stress concentrations or safety margins. - How to Avoid It:
Interpret your results holistically: review von Mises stress, principal stress, displacement, reaction forces, and factor of safety together to get the full picture.
7. Failing to Validate the Simulation
- The Mistake:
Assuming simulation results are always correct without real-world comparison. - Why It Matters:
Simulation is a prediction, not a guarantee. Blind trust in software can be risky. - How to Avoid It:
Validate your simulations with hand calculations, prototype testing, or historical data—especially for new workflows or critical designs.
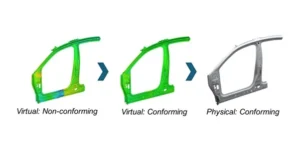
Final Thoughts
SOLIDWORKS Simulation can be a game-changer—but like any powerful tool, it demands careful use. By avoiding these common mistakes, you’ll gain more accurate insights, reduce errors, and maximize your engineering confidence.
Want to explore how simulation can boost your design workflow? Reach out to our experts for a consultation or training session.