Ensuring a product’s reliability throughout its lifecycle is very essential in product design. One of the key factors influencing a product’s durability is fatigue, which refers to the gradual weakening of a material due to repeated stress cycles. As manufacturers aim to develop products that can withstand real-world conditions, fatigue analysis has become a vital tool for predicting a product’s lifespan.
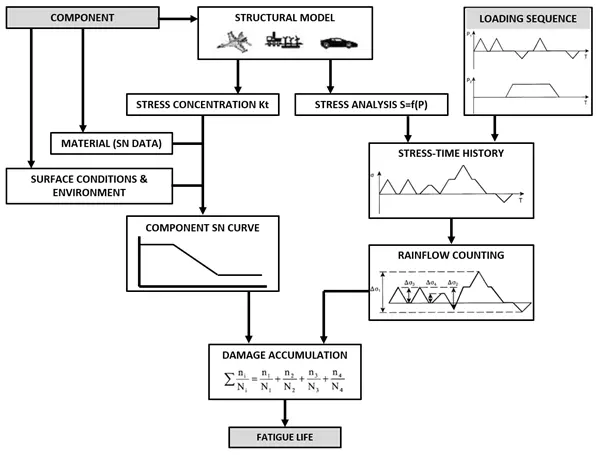
Step-by-Step Guide to Fatigue Analysis in SOLIDWORKS
1. Creation of Model Definition
The first step includes defining the material properties that are critical for fatigue analysis, such as the fatigue limit and endurance strength. These information’s describe the stress level below which a material can theoretically withstand an infinite number of cycles without failing.
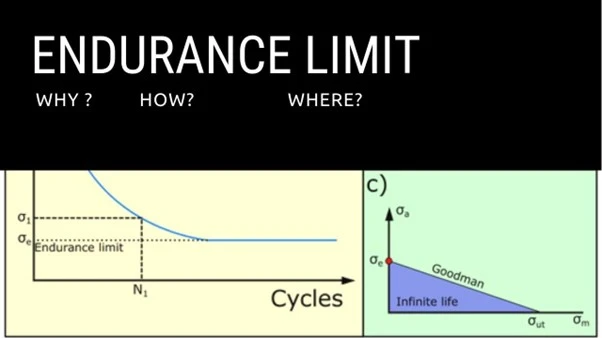
2. Perform Static Analysis
Since fatigue analysis depends on the results of a static study, conducting a static analysis is crucial before performing fatigue analysis. The static analysis provides the stress and displacement data needed for the fatigue simulation. It also helps you understand how your product will perform under normal, constant loading before predicting how repeated stresses will lead to potential failure.
3. Perform Fatigue Analysis
The next step is to set up the fatigue study by selecting the appropriate study type and material model. For example, Constant Amplitude Fatigue assumes uniform load cycles in both magnitude and direction, while Variable Amplitude Fatigue is used when load cycles vary in magnitude, which is common in real-world conditions where loads fluctuate unpredictably. Additionally, choosing the right fatigue material model, such as the S-N Curve or Miner’s Rule, is crucial for ensuring the accuracy of the fatigue study.
4. Identify Loading Conditions
One of the most critical aspects of fatigue analysis is the application of loading conditions. In real-world use, products rarely experience constant, uniform loads; rather, they are subjected to varying cyclic loads over time.
- Cyclic Loads: Apply the loads as cyclic forces to simulate real-world usage. These could include forces that repeat at regular intervals (e.g., car suspension systems) or irregular, fluctuating loads.
- Stress Cycles: The number of stress cycles a product will undergo in its life is essential for determining how fatigue will accumulate over time.
- Real-World Load Variations: Be sure to account for potential variations in loading conditions during the product’s lifecycle, as fatigue is highly dependent on these variations.
5. Interpretation of Result
Once all conditions are defined, it’s time to run the simulation. Normally, simulation software will provide a fatigue damage percentage plot for each region of the product, allowing you to evaluate the area’s most at risk for failure. This value indicates how much damage has occurred due to the applied cyclic loads. A higher percentage means a higher likelihood of failure.
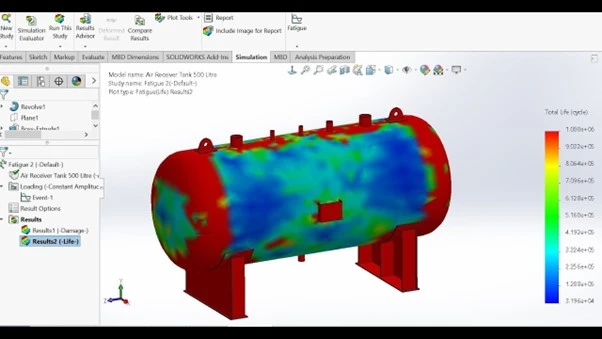
Best Practices for Accurate Fatigue Analysis
To ensure accurate and reliable results, it’s important to follow some best practices when conducting fatigue analysis:
✅ Selecting the Right Mesh Size: A finer mesh provides more detailed results, but it also requires more computational resources. A balance between mesh size and simulation time is key.
✅ Avoiding Singularity Errors: Ensure that your model is properly constrained to avoid unrealistic results caused by singularities, which can occur at points of extreme geometry changes.
✅ Understanding Stress Concentrations: Pay close attention to areas where stresses are concentrated, such as fillets or holes, as these are more likely to experience fatigue failure.
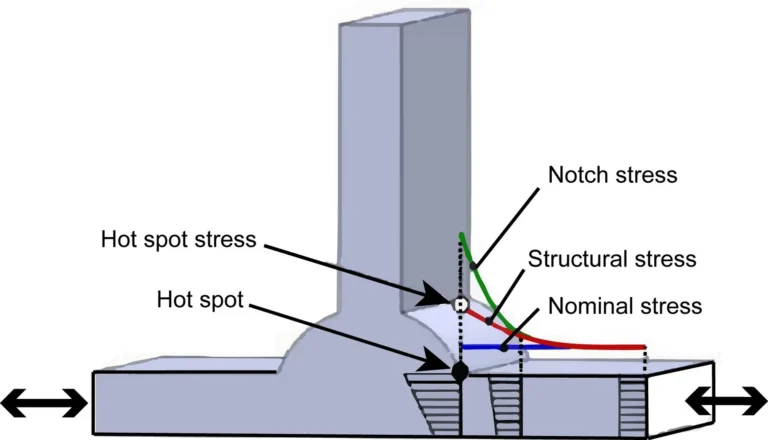
Application
Consider the automotive industry, where fatigue analysis is critical for components like suspension systems and engine parts. By performing accurate fatigue simulations, manufacturers can prevent catastrophic failures and ensure that vehicles meet safety and performance standards throughout their lifespan.
By leveraging fatigue analysis tools, designers can create more durable products, leading to fewer failures, longer product lifespans, and ultimately, more satisfied customers
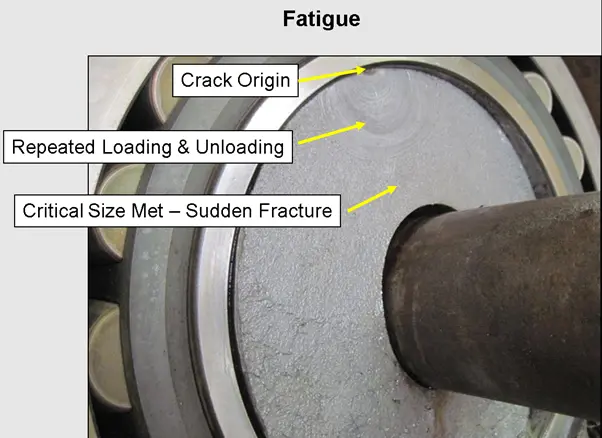
Want to see how cutting-edge simulations can enhance product durability? Discover how SOLIDWORKS Simulation helps engineers design tougher, more reliable devices. Contact us today for expert guidance or explore SOLIDWORKS Simulation to revolutionize your product development!